De-Waxing & CoreLeaching Autoclaves
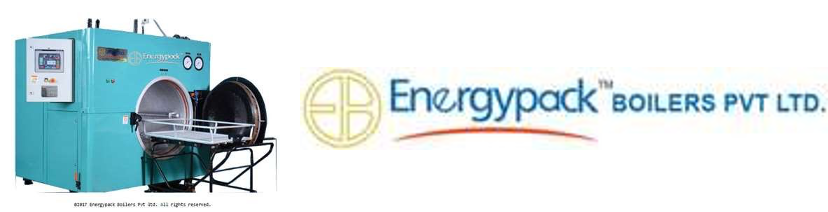
De-waxing and CoreLeaching Autoclaves are used to remove wax from cores and leach metals from ores. They are typically large, pressurized vessels that are heated to high temperatures. The wax or metal is then dissolved in a solvent, which is then removed from the autoclave. De-waxing and CoreLeaching Autoclaves are used in a variety of industries, including the automotive, aerospace, and mining industries.
De-waxing Autoclaves are used to remove wax from cores that are used in the manufacturing of castings. The wax is melted and then removed from the core, leaving behind a clean, dry core that is ready to be used.
CoreLeaching Autoclaves are used to leach metals from ores. The ore is placed in the autoclave and a solvent is added. The solvent dissolves the metal from the ore, which is then removed from the autoclave. The metal can then be refined and used in a variety of applications.
De-waxing and CoreLeaching Autoclaves are essential tools for a variety of industries. They are used to remove wax from cores, leach metals from ores, and clean and prepare materials for use in manufacturing.
3 & 5 Axis LASER, Oxy Fuel & Water JET Cutting

3 and 5 axis laser cutting, oxy fuel cutting, and water jet cutting are all methods of cutting materials. Laser cutting uses a high-powered laser beam to cut through materials, while oxy fuel cutting uses a combination of oxygen and fuel to create a very hot flame that cuts through materials. Water jet cutting uses a high-pressure stream of water to cut through materials.
Each of these methods has its own advantages and disadvantages. Laser cutting is very precise and can be used to cut a variety of materials, but it can be expensive. Oxy fuel cutting is less expensive than laser cutting, but it is not as precise and can only be used to cut certain materials. Water jet cutting is very precise and can be used to cut a variety of materials, but it is the most expensive of the three methods.
The best method for cutting a particular material will depend on the material, the desired level of precision, and the budget.
TurnKey Investment Casting Plants
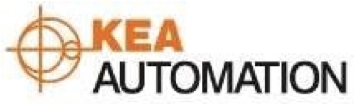
Turnkey investment casting plants are a type of manufacturing facility that is designed to be fully operational and ready to produce castings as soon as it is installed. These plants are typically built to the specifications of the customer and can be customized to produce a variety of different types of castings. Turnkey investment casting plants offer a number of advantages over traditional casting methods, including:
- Increased efficiency: Turnkey investment casting plants are designed to be highly efficient, which can lead to significant cost savings.
- Improved quality: Turnkey investment casting plants are typically equipped with state-of-the-art equipment that can produce castings with very high levels of quality.
- Reduced lead times: Turnkey investment casting plants can be built and commissioned in a fraction of the time it takes to build a traditional casting facility.
If you are considering investing in a casting facility, a turnkey investment casting plant may be the right option for you.